Sika MonoTop®-4012
Sika MonoTop®-4012 is a 1-part, fibre-reinforced, low-shrinkage, cementitious repair mortar. It contains recycled supplementary cementitious materials and can therefore contribute to reducing the carbon footprint of the application.
- Uses recycled raw materials
- Layer thickness 6–120 mm
- Sulphate-resistant
- Hand and machine application (wet spray technique)
- Easy to apply
- Very low shrinkage
- Dust-reduced
- Good resistance to sea water
- Does not require a bonding primer
- Low permeability
- A1 fire rating
- Class R4 of EN 1504-3
- Resistant to sulphuric acid attack (meets the requirements of exposure class XWW3 according to EN 19573)
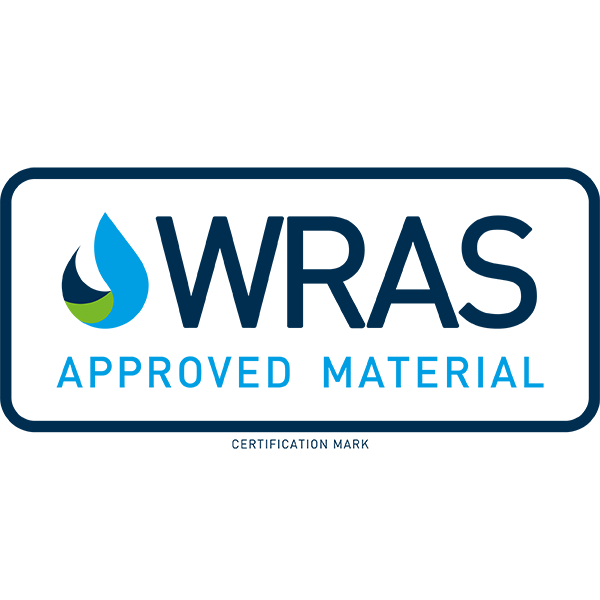
Usage
Sika MonoTop®-4012 is used to repair all types of reinforced concrete structures and components for:- Buildings
- Civil engineering structures
- Dams
- Marine structures
- Domestic and municipal sewage treatment plants including wastewater
- Restoration work (Principle 3, method 3,1 and 3,3 of EN 1504-9). Repair of spalling and damaged concrete in infrastructure and superstructure works.
- Structural strengthening (Principle 4, method 4,4 pf EN 1504-9). Increasing the bearing capacity of the concrete structure by adding mortar.
- Preserving or restoring passivity (Principle 7, method 7,1 and 7,2 of EN 1504-9). Increasing cover with additional mortar and replacing contaminated or carbonated concrete
- Concrete exposure classes XC 1-4, XF 1-4, XD 1-3, XS 1-3 and XA 1-3 as described in EN 206
- The Product may only be used by experienced professionals.
Advantages
- Uses recycled raw materials
- Layer thickness 6–120 mm
- Sulphate-resistant
- Hand and machine application (wet spray technique)
- Easy to apply
- Very low shrinkage
- Dust-reduced
- Good resistance to sea water
- Does not require a bonding primer
- Low permeability
- A1 fire rating
- Class R4 of EN 1504-3
- Resistant to sulphuric acid attack (meets the requirements of exposure class XWW3 according to EN 19573)
Packaging
Standard bag | 25 kg |
Refer to the current price list for available packaging variations.
Colour
Grey
Product Details
ENVIRONMENTAL INFORMATION
Contributes towards satisfying Materials and Resources (MR) Credit: Building product disclosure and optimization — Environmental Product Declarations under LEED® v4 — 1 point
Contributes towards satisfying Materials and Resources (MR) Credit: Building Product Disclosure and Optimization — Sourcing of Raw Materials under LEED® v4 — 1 point
Contributes towards satisfying Materials and Resources (MR) Credit: Building Product Disclosure and Optimization — Material Ingredients under LEED® v4 — 1 point
Specific Environmental Product Declaration (EPD) in accordance with EN 15804. EPD independently verified by BRE Global
Bewertungsbestätigung, Sika MonoTop-4012, ecobau
eurofins VOC Emission Indoor Air Comfort Sika MonoTop-4012
APPROVALS / STANDARDS
CE marking and declaration of performance based on EN 1504-3:2005 Products and systems for the protection and repair of concrete structures — Structural and non-structural repair
Klassifizierung / Classification Brandverhalten / Reaction to fire EN 13501-1
Specific electrical resistivity DIN EN ISO 12696, Sika MonoTop®-4012, OST
Tensile bond strength after vibrational stress DAfStb guideline, Sika MonoTop-4012, kiwa, Test report No. P 11864-1-E
Sulphate Resistance ÖNORM B 3309-1, Sika MonoTop-4012, HARTL, No. 013108/2
Sewage Network Test Report DIN 52108, LPM, No. A-49 ́492-6.1E
Resistance to alkali aggregate reaction SIA 262/1, Sika MonoTop®-4012, TFB, Test Report No. 232336-01K
Physical test of the frost deicing salt resistance BE II FT, VSS 40 464
Adhesive tensile strength in overhead application
Chemical Base
Sulphate-resistant cement, supplementary cement replacement, selected aggregates and additives
Shelf Life
Standard bag | 12 months from date of production |
Storage Conditions
The Product must be stored in original, unopened and undamaged sealed packaging in dry conditions at temperatures between +5 °C and +35 °C. Protect the Product from direct sunlight. Always refer to the packaging.
Refer to the current Safety Data Sheet for information on safe handling and storage.
Maximum Grain Size
2 mm
Soluble Chloride Ion Content
≤ 0,05 % | (EN 1015-17) |
System Structure
Layer | Function | Product |
Optional: Bonding primer / Reinforcement corrosion protection | Normal use | Sika MonoTop®-1010 |
Optional: Bonding primer / Reinforcement corrosion protection | Demanding requirements | SikaTop® Armatec®-110 EpoCem® |
Concrete repair mortar | High strength requirements | Sika MonoTop®-4012 |
Optional: Levelling mortar | Normal use | Sika MonoTop®-3020 |
Optional: Levelling mortar | Demanding requirements | Sikagard®-720 EpoCem® |
Abrasion Resistance
Wear Resistance Böhme, wet procedure | < 12 cm3/50 cm2 |
Compressive Strength
Class R4 | (EN 1504-3) |
Time | Compressive strength |
1 day | 19 MPa |
7 days | 43 MPa |
28 days | 56 MPa |
Modulus of Elasticity in Compression
≥ 20 GPa | (EN 13412) |
Flexural Strength
Time | Tensile strength in flexure |
1 day | 4.4 MPa |
7 days | 7.0 MPa |
28 days | 8.0 MPa |
Shrinkage
+20 °C and 65 % relative humidity at 28 days | 500 μm/m |
Restrained Shrinkage / Expansion
≥ 2.0 MPa | (EN 12617-4) |
Tensile adhesion strength
≥ 2.0 MPa | (EN 1542) |
Thermal Compatibility
≥ 2.0 MPa (Part 1 - Freeze-Thaw) | (EN 13687-1) |
Coefficient of Thermal Expansion
16 × 10–6 1/K | (EN 1770) |
Reaction to Fire
Class A1 | (EN 13501-1) |
Capillary Absorption
≤ 0.5 kg∙m-2·h-0.5 | (EN 13057) |
Water Penetration under Pressure
10 mm | (EN 12390-8) |
Chloride Ion Diffusion Resistance
Low < 2000 Coulombs | (ASTM C1202) |
Carbonation Resistance
dk ≤ control concrete MC (0.45) | (EN 13295) |
Electrical Resistivity
< 100 kΩ·cm | (ISO 12696) |
Application
Mixing Ratio
3.75 to 3.9 L of water for a 25 kg bag
Layer Thickness
Orientation | Minimum | Maximum |
Horizontal | 6 mm | 120 mm |
Vertical | 6 mm | 85 mm (120 mm in localised areas) |
Overhead | 6 mm | 30 mm (50 mm in localised areas) |
Product Temperature
Maximum | +30 °C |
Minimum | +5 °C |
Ambient Air Temperature
Maximum | +30 °C |
Minimum | +5 °C |
Substrate Temperature
Maximum | +30 °C |
Minimum | +5 °C |
Pot Life
At +20 °C | 60 minutes |
Pot life depends on temperature
Note: Pot life will be shorter at higher temperatures. Pot life will be longer at lower temperatures.
Fresh mortar density
2.1 kg/L | (EN 1015-6) |
Consumption
1.9 kg powder per m2 per mm
Note: Consumption data is theoretical and does not allow for any additional material due to surface porosity, surface profile, variations in level, wastage or any other variations. Apply the Product to a test area to calculate the exact consumption for the specific substrate conditions and proposed application equipment.
Yield
13.7 L of mortar per 25 kg bag
Note: Consumption data is theoretical and does not allow for any additional material due to surface porosity, surface profile, variations in level, wastage or any other variations. Apply the Product to a test area to calculate the exact consumption for the specific substrate conditions and proposed application equipment.
EQUIPMENT
Select the most appropriate equipment required for the project.
SUBSTRATE PREPARATION EQUIPMENT
Mechanical hand-held tools for spot repairs
High- or ultra-high-pressure water blasting equipment
STEEL REINFORCEMENT EQUIPMENT
Abrasive blast cleaning equipment
High-pressure water blasting equipment
MIXING EQUIPMENT
Clean mixing containers
Small quantities: low-speed electric single or double-paddle mixer (< 500 rpm).
Large quantities: forced action mixer
APPLICATION EQUIPMENT
Hand-applied: plasterer's hawk, trowel
Wet spray: All-in-one mixing and spraying machine, or separate spraying machine and all associated ancillary equipment to suit application volumes. Suitable machines include the PFT N2V, Putzmeister S 5, Wagner PC15, and Inotec inoBEAM F50.
FINISHING EQUIPMENT
Trowel (PVC or wooden)
Sponge
SUBSTRATE PREPARATION
CONCRETE
- Clean the substrate thoroughly so it is free from dust, loose material, surface contamination and material which reduces adhesion, prevents suction or wetting by the repair materials.
- Remove delaminated, weak, damaged and deteriorated concrete and where necessary, sound concrete. Remove using mechanical hand-held tools, high or ultra-high-pressure water blasting equipment.
- Remove sufficient concrete from around corroded reinforcement to allow cleaning, application of a corrosion protection coating (where required) and compaction of the concrete repair mortar.
- Prepare repair surface areas in simple square or rectangular layouts to avoid shrinkage stress concentrations and cracking while the repair material cures. This can also avoid structural stress concentrations from thermal movement and loading during the service life.
STEEL REINFORCEMENT
- Remove rust, scale, mortar, concrete, dust and other loose and deleterious material which reduces bond or contributes to corrosion.
- Prepare surfaces to bright steel, Sa 2 (ISO 8501-1), using abrasive blast cleaning or high-pressure water blasting equipment.
MIXING
HAND APPLIED AND WET SPRAY APPLICATION
- Pour the minimum amount of water into a suitable clean mixing container or equipment.
- Gradually add the powder to the water while stirring slowly.
- Mix thoroughly for at least for 3 minutes, add additional water if necessary. Note Do not add more water than the maximum specified amount.
- Adjust to the required consistency to achieve a smooth consistent mix.
- Check the consistency after every mix.
APPLICATION
IMPORTANT
Strictly follow installation procedures
Strictly follow installation procedures as defined in Method Statements, application manuals and working instructions which must always be adjusted to the actual site conditions.
IMPORTANT
Risk of cracking due to exposure to frost
- Protect freshly applied material from freezing and frost.
IMPORTANT
Risk of cracking due to application in direct sun or strong winds
- Do not apply the Product in direct sun, strong winds or both.
IMPORTANT
Risk of reduced strength gain and impaired physical properties in cold weather
Take the following measures in cold weather:
- Store bags in a warm environment.
- Use warm mixing water to assist with achieving strength gain and maintaining physical properties.
IMPORTANT
Risk of cracking and impaired physical properties in hot weather
Take the following measures in hot weather:
- Store bags in a cool environment.
- Use cold mixing water to assist with controlling the exothermic reaction to reduce cracking and to maintain physical properties.
REINFORCEMENT CORROSION PROTECTION COATING
- Where a reinforcement coating is required, apply to the whole exposed circumference Sika MonoTop®-1010 or SikaTop® Armatec®-110 EpoCem®. Refer to the individual Product Data Sheets.
BONDING PRIMER
On a well prepared and roughened substrate or for a sprayed application, a bonding primer is generally not required.
When a bonding primer is required to achieve the required adhesion values, use Sika MonoTop®-1010 or SikaTop® Armatec®-110 EpoCem®. Refer to the individual Product Data Sheets.
REPAIR MORTAR – MANUAL APPLICATION
IMPORTANT
Poor Product performance due to insufficient substrate pre-wetting
Insufficient substrate saturation prior to application will cause the mortar to not gain its full mechanical properties.
- Only apply the Product to stable, prepared substrates.
- Thoroughly pre-wet the prepared substrate for a minimum of 2 hours before application.
- Keep the surface wet and do not allow to dry.
- The final pre-wetted surface must achieve a dark matt appearance (saturated surface dry).
IMPORTANT
Sagging or slumping of built up layers
Allow each layer to slightly harden and remain wet before applying subsequent layers.
- Remove excess water from within the surface pores and cavities with a clean sponge.
- Make a scratch coat using the repair mortar Product.
- Apply the scratch coat over the complete substrate surface to form a thin layer to fill surface pores or cavities.
- Apply the repair mortar Product on to the scratch coat wet on wet, without forming voids, and observing the minimum and maximum layer thicknesses.
REPAIR MORTAR – SPRAYED APPLICATION – WET SPRAY
IMPORTANT
Poor Product performance due to insufficient substrate pre-wetting
Insufficient substrate saturation prior to application will cause the mortar to not gain its full mechanical properties.
- Only apply the Product to stable, prepared substrates.
- Thoroughly pre-wet the prepared substrate for a minimum of 2 hours before application.
- Keep the surface wet and do not allow to dry.
- The final pre-wetted surface must achieve a dark matt appearance (saturated surface dry).
IMPORTANT
Sagging or slumping of built up layers
Allow each layer to slightly harden and remain wet before applying subsequent layers.
- Remove excess water from within the surface pores and cavities with a clean sponge.
- Place the wet mixed repair mortar into the spraying equipment.
- Spray the repair mortar onto the pre-wetted substrate between the minimum and maximum layer thicknesses without the formation of voids.
SURFACE FINISHING BY HAND
IMPORTANT
Risk of discolouration and cracking due to adding water during surface finishing
- Do not add water during the surface finishing.
IMPORTANT
Surface cracking due to rapid moisture loss
In draughty areas, open spaces, at temperatures less than +10 °C or in very dry climates, early plastic shrinkage cracks may occur.
- Confirm substrate moisture content, product, substrate and air temperatures prior to application.
- Allow the mortar to surface harden.
- Surface finish to the required surface texture using a stainless steel, steel, PVC or wooden float.
CURING TREATMENT
Protect fresh mortar immediately from premature drying using an appropriate curing method, such as curing compound, moist geotextile membrane or polythene sheet.
Do not use curing compounds if they could adversely affect subsequently applied products and systems.
CLEANING OF TOOLS
Clean all tools and application equipment with water immediately after use. Hardened material can only be removed mechanically.